According to the Renewable Fuel Standard in the U.S. Energy Independence and Security Act of 2007 – also known as the 2007 energy bill, the United States is required to produce 16 billion gallons of cellulosic biofuel per year by 2022.
The term “cellulosic biofuel” refers to renewable fuel derived from any cellulose, hemicellulose, or lignin that is derived from renewable biomass. More specifically, feedstocks for producing this biofuel include nonfood-based sources like grasses, agricultural crop residues, logging residues, and sawdust.
In 2013, according to the EPA, the U.S. produced 0.51 million gallons of cellulosic biofuel. Furthermore, the Renewable Fuels Association indicates commercial plants were opened in 2014-2015 that have 75 million gallons of capacity.
Scaling up production of cellulosic biofuels will require solutions to significant logistics and processing challenges. The movement of large volumes of feedstocks, including their water content, will require numerous trucks utilizing rural roads and bridges, additional rail and barge services, and other burdens on infrastructure.
Raw or unprocessed feedstocks will require large areas for storage plus exhibit wide seasonal fluctuation in availability – and most feedstocks are subject to perishability with time and weather conditions. These forces can lead to formidable issues for road and bridge planning, materials handling and facility requirements. Studies have revealed that logistics costs can represent up to one-third of the cost of producing fuels.
With careful design and planning, improving logistics for the production of cellulosic biofuels could greatly lower the cost of producing cellulosic biofuels, possibly leading to the development of low cost domestic liquid fuel supplies. Cost saving benefits could be found through advancements and developments in storage, densification, and multi feedstock processing technologies.
Traditionally, the processing of feedstocks has taken place in close proximity to the growing or generating location. It is possible that distributed “hubs” of processing and storage could lead to greater efficiencies, and therefore, lower costs all the way to the consumer. It might also be possible to balance the supply in a particular area of variably available feedstocks with a feedstock supply of more consistency.
Dr. Bruce A. McCarl, a Distinguished Professor of Agricultural Economics, is leading a team of engineers and supply chain experts that will prepare two case studies on a broad range of logistics issues related to cellulosic biofuel production. They will address the elements of feedstock logistics and the costs involved with location of production, densification, hauling, storage volume, storage loss, moisture, depots, feedstock diversification, and moisture management.
The study will begin with the development of a listing of the costs of major logistic alternatives to common practices, the potential benefits of adding densification and depots to the process, calculating storage losses and the cost of moisture, as well as the value of diversifying feedstocks. They will also develop a thorough justification of work with comparative budgeting across some simple alternatives and will conceptualize a model to handle diverse alternative logistical, production, and processing scenarios.
Two regions were chosen for the case studies based on the potential availability of feedstocks, as well as switchgrass growing conditions. Both offer feedstocks and lands that are not directly competitive with conventional food crop production.
The first case study area will be a Midwest location – perhaps Indiana – on switchgrass, corn stalks, and wood. The Midwest has existing ethanol production infrastructure as well as a considerable corn residue supply. Additionally, parts of Indiana have substantial areas of marginal lands and stands of trees.
The second case study area will be a southern location in East Texas, focusing on switchgrass and forest products and byproducts. East Texas is in close proximity to large liquid fuels processing facilities that provide supporting infrastructure. Additionally, East Texas has a steady supply of water for production as well as marginal lands and trees. The southern region provides an opportunity to explore longer-duration harvest and storage options because of milder winters.
Both studies will provide a regional analysis and associated modeling to investigate the development of a supply chain, plant location, and spatial feedstock production, storage, and densification. The analysis will consider locations of single or multiple feedstock production in addition to biorefinery operation and feedstock movement, storage, and densification. Finally, the research will factor in regional implications for income, greenhouse gas emissions, energy use, and a wide range of energy production costs.
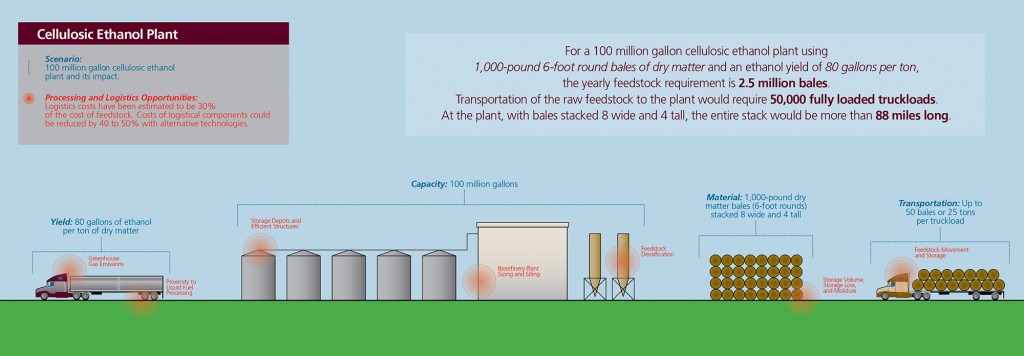