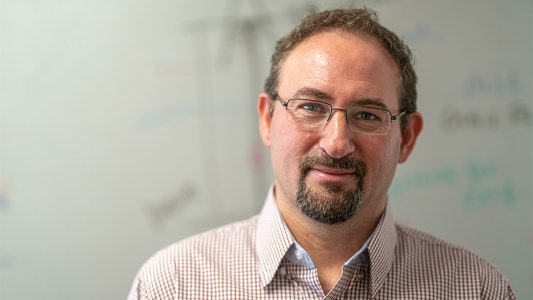
Drilling into the Earth to tap energy reservoirs is expensive and risky. Rapid decisions based on accurate information could reduce equipment failure or accidents and quicken the time it takes to drill a well. Yet, current well imaging only gives a limited, static picture of the underground environment to drilling operators. An autonomous drilling solution could reduce costs and reduce risks to people and equipment.
To improve safety and cut costs, the United States Department of Energy Small Business Innovation Research Program has awarded a Phase I grant to E-Spectrum Technologies and Dr. Eduardo Gildin, associate professor in the Harold Vance Department of Petroleum Engineering at Texas A&M University, to create an advanced advisory system that accurately depicts underground conditions in real time during drilling operations.
E-Spectrum has a hardware package that can be installed behind the drill bit. The software in it currently uses algorithms provided by Gildin to gather and filter data from bit vibrations, speed or sound changes, and temperature or pressure changes. But while the E-spectrum unit can quickly assess underground conditions and refine the data, it cannot do much more.
“The system in the well hole is robust, but has limited space and memory to store and process all the data collected by the sensors,” said Gildin. “With our new algorithm, it processes the information in the hole and transmits the detection of abnormal bit behavior in real time to the surface for review and storage. This way, the surface unit can refine the information to see the conditions in the hole from a 360-degree bird’s eye view and better predict issues so the driller can take action before problems happen.”
Historically, drilling is not associated with sophisticated technology. The harsh environments of geothermal and petroleum reservoirs can be disruptive — that is, as a drill bit travels underground, it chews into challenging rock compositions and encounters high temperature and pressure fluctuations, any of which can severely damage delicate electronics. But even if a technology is designed to survive such harsh conditions, it still must function rapidly. Without real-time data from the underground environment, a drilling operator could force a drill bit into a hard rock formation at higher speeds than what the bit was designed to handle, causing a dangerous and costly reaction.
To solve this problem, E-Spectrum and Gildin have come up with a two-system solution. In addition to the system developed by E-spectrum that operates in deep Earth, where temperatures can reach up to two and a half times the boiling point of water, Gildin has developed a surface-bound detection system. Thus, the underground unit handles the jarring motions of passing through rock while it filters and wirelessly transmits this information about the drill bit vibrations, rotation speed and other measurements to the unit above the ground.
The dysfunction detection system on the surface uses publicly open software. Gildin programmed it to sift through the information and look for abnormalities the drilling operators need to know quickly. For instance, if a bit strongly vibrates while traveling through a particular rock, the system knows to warn the operator, who will slow the bit speed and reduce the chance of equipment failure. At other times, the bit could smoothly cut through, meaning the speed could be increased. Since the programming is based on machine learning, the surface system records these patterns of vibration and bit behavior and learns from them.
Gildin noted that his software can pinpoint drill bit position and unusual behavior faster and with better accuracy than current systems.After the successful completion of Phase I, E-Spectrum and Gildin plan to apply for additional funding to move forward with Phase II in February 2020. In Phase II, Gildin will prepare the surface system not just to monitor what is going on underground, but come up with suggestions for the drilling operator, should problems arise. This updated advisory system will be designed to assist the operator so that decisions are made faster without losing accuracy.
“Right now, this is an open-loop advisory system, telling drillers what is happening, what might happen and why,” said Gildin. “It gives drillers a chance to adjust their plan of attack during drilling manually. The closed-loop automated system is next, where action can be taken by machines, though still guided and approved by human choice. It also opens up the door to autonomous drilling in a way that the operation can be done with minimal human intervention.”
Gildin said that in the future, as companies gather more data, the open-source software can be adapted to many other drilling applications.
“No matter what hardware system is in the hole, the downhole algorithms and surface system functions can use gathered data and machine learning to improve the drilling process,” said Gildin. “This can advise in any drilling application, whether using drill bits or water jets, on the Earth or even remotely in space.”
This article originally appeared at: https://engineering.tamu.edu/news/2020/01/researchers-create-advanced-advisory-system-that-opens-door-to-autonomous-drilling.html